Vendor Operational Risks to Watch for (and How to Protect Yourself)
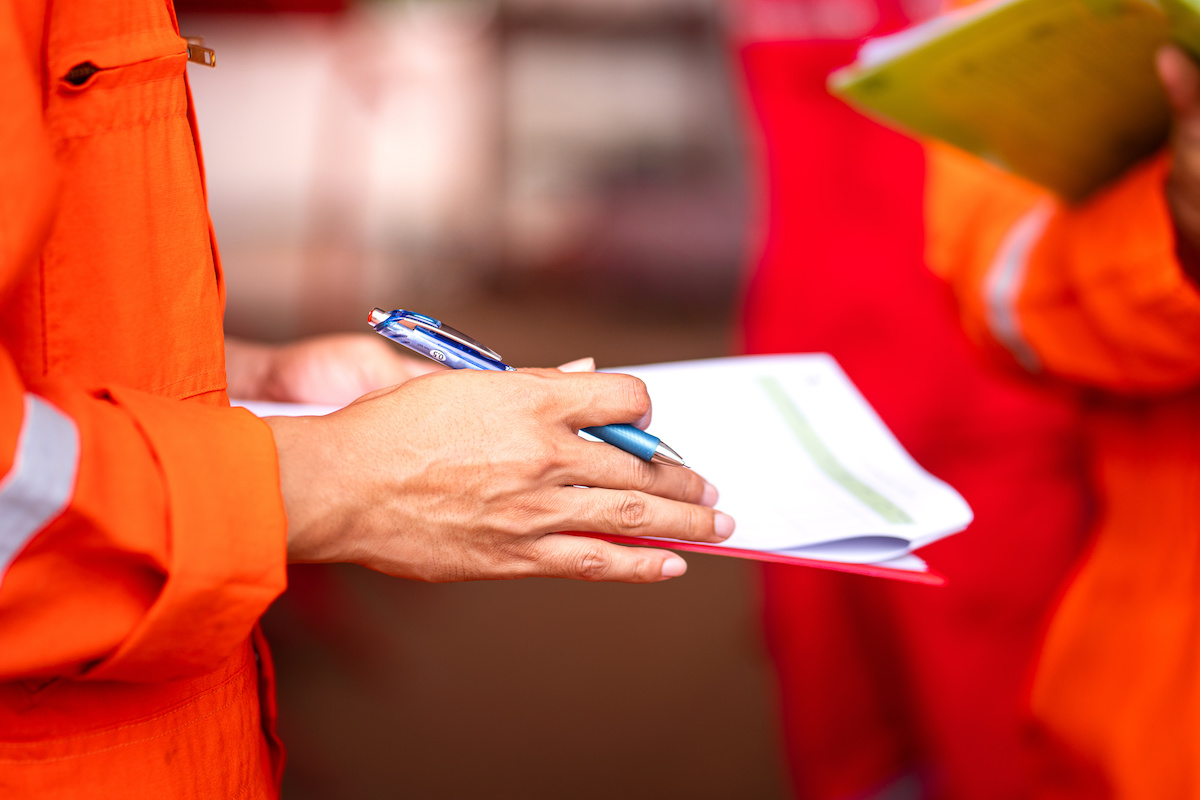
For some companies, a risk event can almost seem like it’s popped up out of nowhere. A sudden supplier failure or catastrophic event can take you by surprise — and there’s no time to waste in fixing it.
Whatever your business structure or industry, it's essential that you understand where your firm stands with operational risk management.
Here, we'll help you develop your understanding of operational risk, what causes it, why it matters, and how your organization can manage operational risks in your supply chain.
The Facts About Operational Risk
The Basel Committee on Banking Supervision defines operational risk as "the risk of loss resulting from inadequate or failed internal processes, people and systems, or from external events."
Although this definition specifically applies to financial institutions, it can also apply when a business relies on third parties for critical business needs.
Outsourcing can bring cost savings and efficiency, but it also opens your business operations to potential risks. Whether a third party’s helping with technology and software services, financial services, or manufacturing, every organization should have an operational risk management process as part of its third-party vendor risk mitigation strategy.
Why Does Operational Risk Matter?
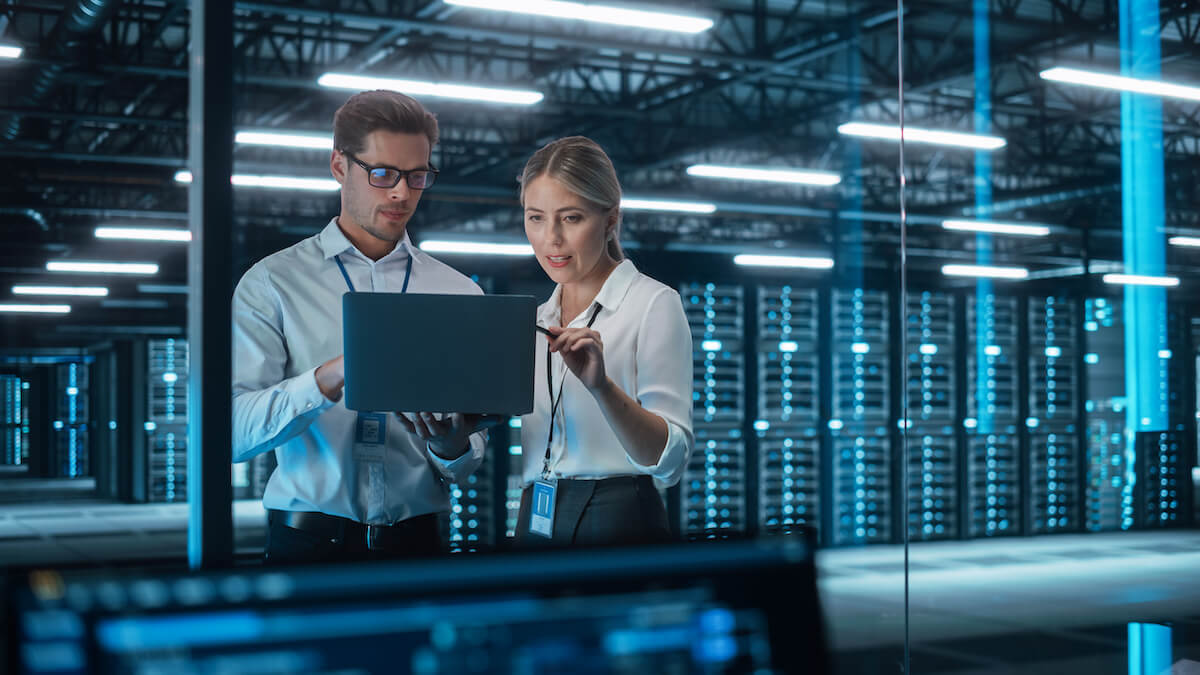
If your business relies more and more on outsourced service providers, it's crucial to take a closer look at how effectively your suppliers are managing their own business risks.
Operational risks in your supply chain can have serious financial, reputational, and legal consequences. When vendors’ critical business processes are disrupted, that system failure can affect your business too.
For example, many organizations use third-party service providers for technology-related projects or services. But if something goes wrong with one of these outsourced providers, your organization could be left holding the bag for your customers' financial losses.
These losses could range from the cost of repairing or replacing faulty equipment to the cost of compensating customers in the event of a data leak.
A bad outsourcing experience doesn’t just affect your bottom line — it can drag you into the court of public opinion too.
Examples of Vendor Operational Risks
We can’t say it enough: Your vendors’ risks can become threats to your own company.
Let’s say your outsourced IT system provider from our earlier example has weak cybersecurity practices. This can leave your company vulnerable to a breach in your own IT infrastructure. If this happens, it’ll become harder to deliver services to your customers, costing you in terms of both reputational risk and financial risk.
Take a recent example: In 2020, vendor Capgemini made a security error that led to a significant customer data leak and operational losses of about $7 million for a Singaporean gaming firm.
On top of lost revenue and opportunities because of downtime, situations like these leave your business open to other legal and financial consequences such as regulatory fines, litigation costs, and loss of customer trust and loyalty.
Other operational risk examples include:
- Contract breaches: When vendors don't fulfill their contractual obligations on time or within budget, it can be harder for you to deliver products and services to your customers.
- Security breaches: If a vendor can’t maintain robust security practices to protect customer data and other sensitive information in their possession, this can put your customers at risk and create liabilities for your organization.
- Service disruptions: Your business is at risk of financial loss when a vendor experiences a service disruption because of risk events including natural disasters, cybercrime attacks, human error, and more.
- Supplier bankruptcies or insolvency: A key vendor may go bankrupt for several reasons, including poor business decisions or unexpected changes in economic conditions. If this happens, your organization might not be able to deliver on your promises to your customers.
- Market risk: When markets change because of unforeseen economic circumstances or other external factors beyond your control, it can lead to volatility in the supply of raw materials and/or products from your vendors.
- Regulatory changes: Changes in regulatory requirements can negatively affect an unprepared supply chain, particularly if these changes lead to increased monitoring by your regulators. This can increase your administrative burden and lead to additional expenses as you implement the right controls and procedures.
What Causes Operational Risk in Supply Chains?
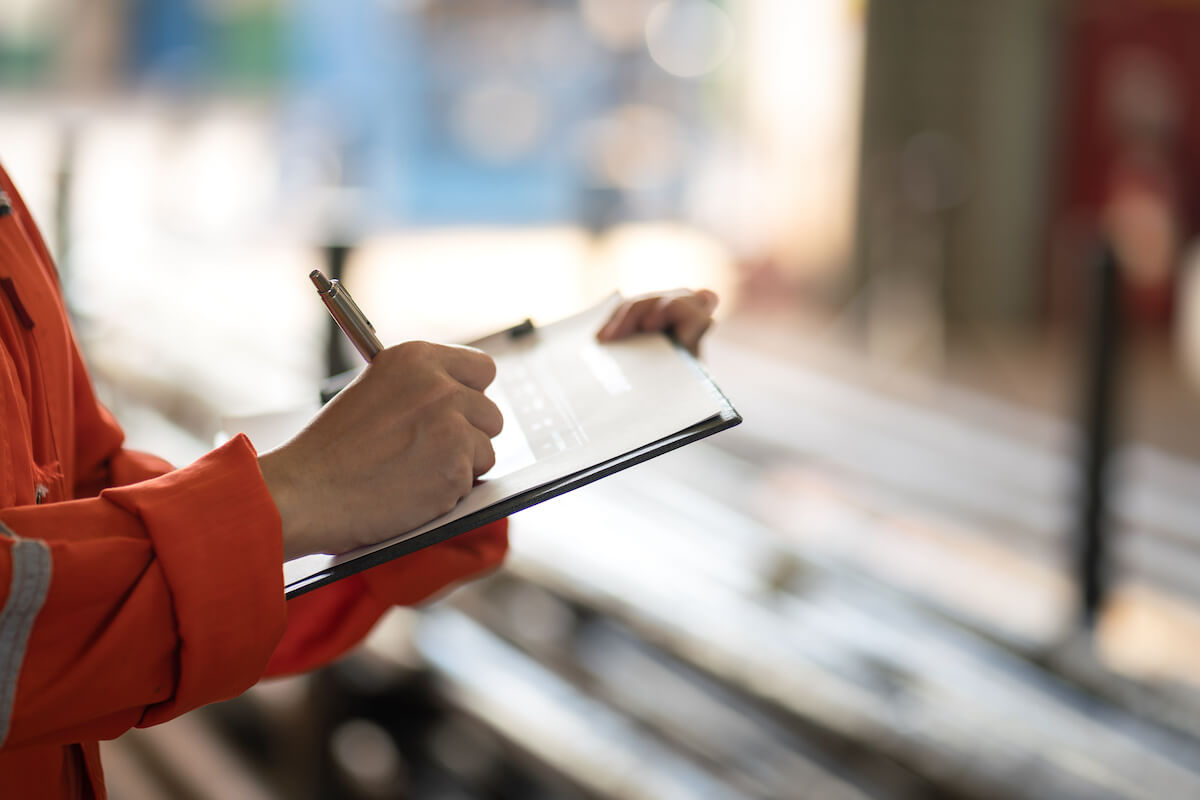
There are several factors that can influence an organization's ability to prevent and control losses due to operational risk factors, including:
- Lack of visibility: A lack of visibility over your third-party network makes it difficult to identify and manage specific risks. This is especially true if your company uses many service providers that aren't fully integrated into your vendor ecosystem.
- Improper or insufficient personnel training: A team's inability to accurately assess its vendors’ risk profiles can lead to procurement mistakes and a negative impact on vendor quality. Without the right supervisory input, the lack of qualified personnel to oversee your vendor management can also cause unsatisfactory relationships with vendors.
- Human error: If your organization isn't prepared to manage its third-party relationships effectively, it's easy for human error to creep in. Of course, careless mistakes can sink your vendor relationships as well.
- Weak risk management processes and controls: Poor risk management processes and a lack of internal controls can leave your business wide open to potential financial losses and other negative outcomes like internal fraud, theft, errors, and breach of contract.
- Reduced focus on compliance: If your senior management team has kept compliance on the back burner for your third-party management program, your firm may be subject to significant fines and other penalties.
- External risk events: Natural disasters, pandemics, acts of war or terrorism, external fraud, and climate risk can all contribute to your operational risk.
How to Reduce Your Organization's Operational Risk Exposure
Poorly assessed and managed risks are a drain on your business. But strong operational risk management processes will help to protect your business and allow you to better fulfill your commitments to customers and other stakeholders.
An effective operational risk management system should help to create a culture of risk awareness for decision-making within your organization. Once your team’s leveled up in terms of risk awareness, you’ll have more risk control in all areas of your business practices — and know how to meet regulatory and international standards.
While it's impossible to get rid of all risky business completely, here are some ways to identify and mitigate potential operational risks in your supply chain:
- Work with key stakeholders to develop your operational risk management framework: Building an operational risk management program starts with understanding your organization’s risk appetite and risk tolerance. Once you know the greatest areas of concern you need to address, you can decide on the right mitigation strategies to use in different business units.
- Use key risk indicators (KRIs): KRIs give your team quantifiable metrics for risk measurement. You can track these over time to understand when your risk might be increasing. For example, increased worker strikes could affect the production output of a manufacturing vendor or the ability to deliver goods on time for a logistics vendor. Both scenarios can wreak havoc on your profitability.
- Conduct regular vendor risk assessments: Regular vendor risk assessments help you see changing risk levels in your supply chain. The assessment process highlights high-risk vendors and areas for improvement so you can take steps to protect your business.
- Practice scenario analysis: Develop different loss event scenarios that could affect your business activities and prepare responses accordingly so that your team can respond quickly and effectively in real-time.
- Develop and implement a robust business continuity plan: Maintaining a strong business continuity plan helps you maintain control over critical business processes during difficult situations, helping to minimize any disruption to operations.
- Strengthen communication lines with your suppliers: Building strong relationships with your key suppliers will help your business to better manage its exposure to various risk factors. It’ll also help you see more potential risks across your supply chain, so both parties can better prepare for unexpected events.
- Keep evaluating your operational risk management program over time: Maintain your operational risk management programs with frequent self-assessment and reviews to ensure your risk management methodologies work just as you wanted them to.
Use automated vendor management platforms to reduce human error and increase risk visibility. Thoughtless mistakes can happen more and more as you place greater demands on your team. Those errors have huge repercussions and can cost an organization in compliance fines, reputation, and ultimately lost business. With automation and 24/7 monitoring, a central vendor management platform helps protect your organization by reducing human errors and offering greater visibility into your risk areas
Vendor Operational Risks to Watch for (and How to Protect Yourself)
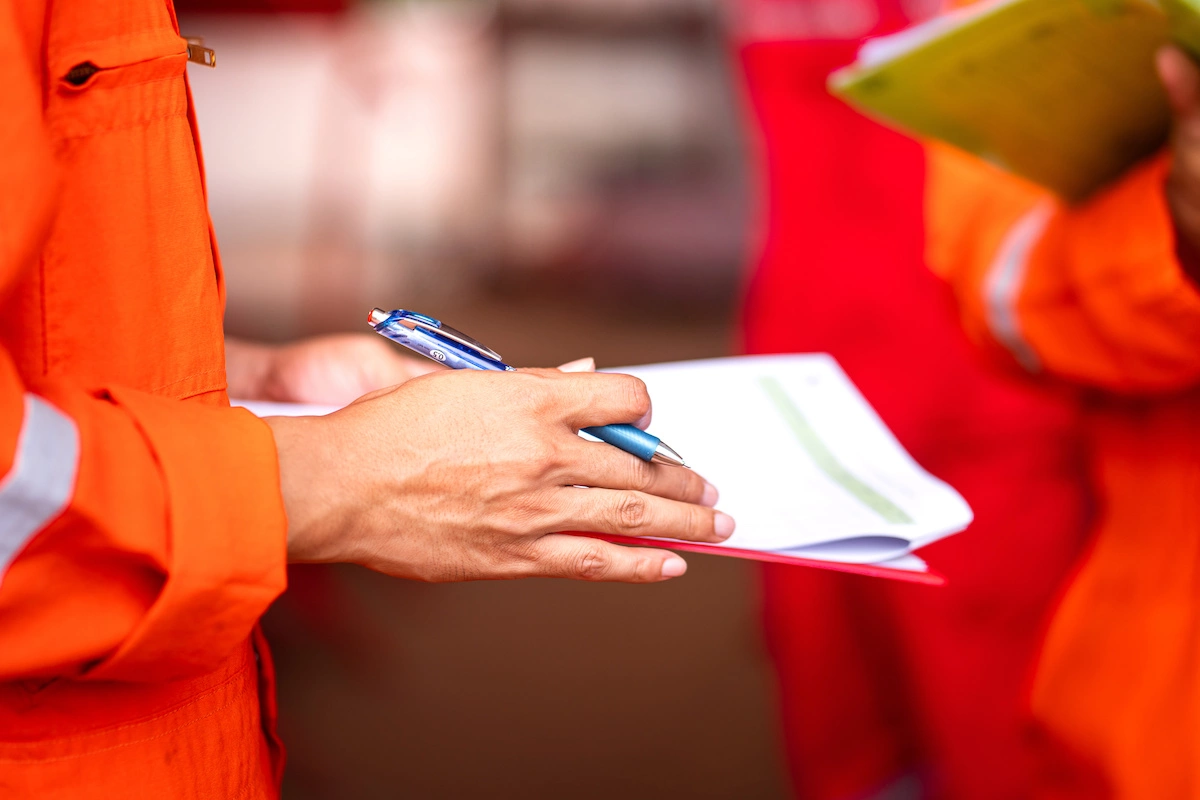
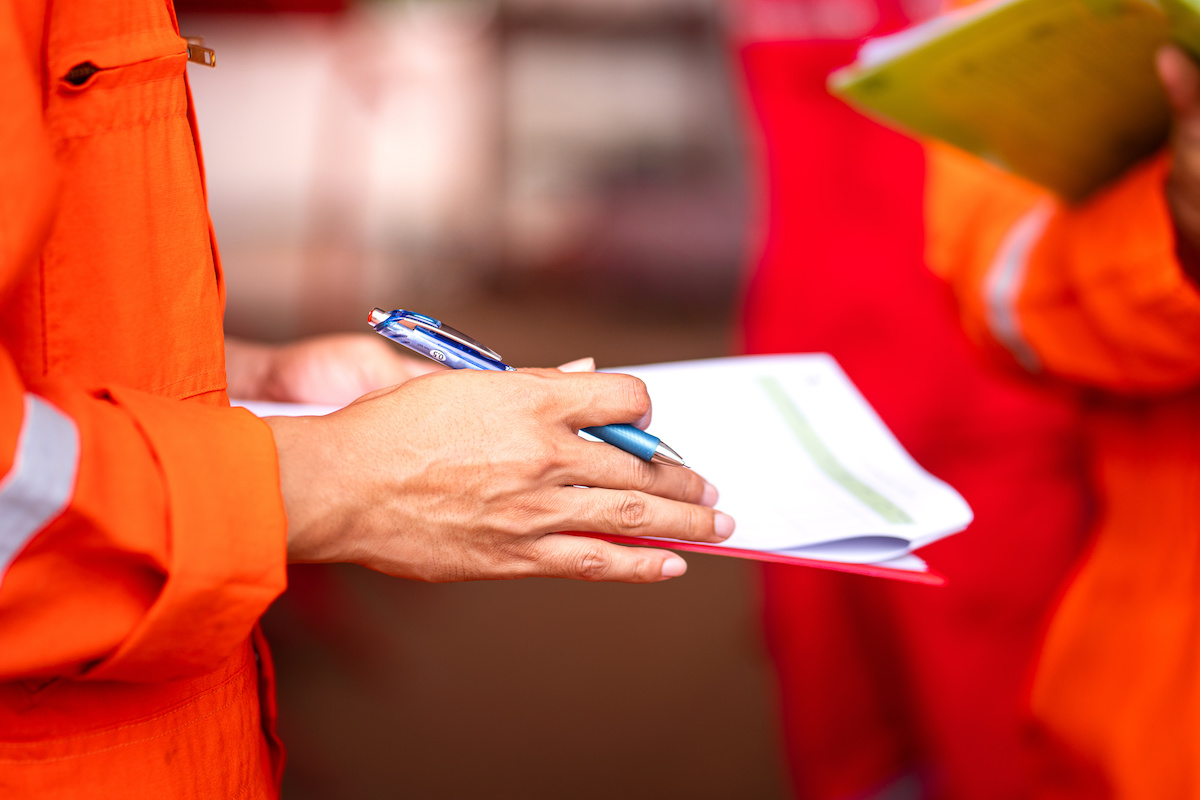
For some companies, a risk event can almost seem like it’s popped up out of nowhere. A sudden supplier failure or catastrophic event can take you by surprise — and there’s no time to waste in fixing it.
Whatever your business structure or industry, it's essential that you understand where your firm stands with operational risk management.
Here, we'll help you develop your understanding of operational risk, what causes it, why it matters, and how your organization can manage operational risks in your supply chain.
The Facts About Operational Risk
The Basel Committee on Banking Supervision defines operational risk as "the risk of loss resulting from inadequate or failed internal processes, people and systems, or from external events."
Although this definition specifically applies to financial institutions, it can also apply when a business relies on third parties for critical business needs.
Outsourcing can bring cost savings and efficiency, but it also opens your business operations to potential risks. Whether a third party’s helping with technology and software services, financial services, or manufacturing, every organization should have an operational risk management process as part of its third-party vendor risk mitigation strategy.
Why Does Operational Risk Matter?
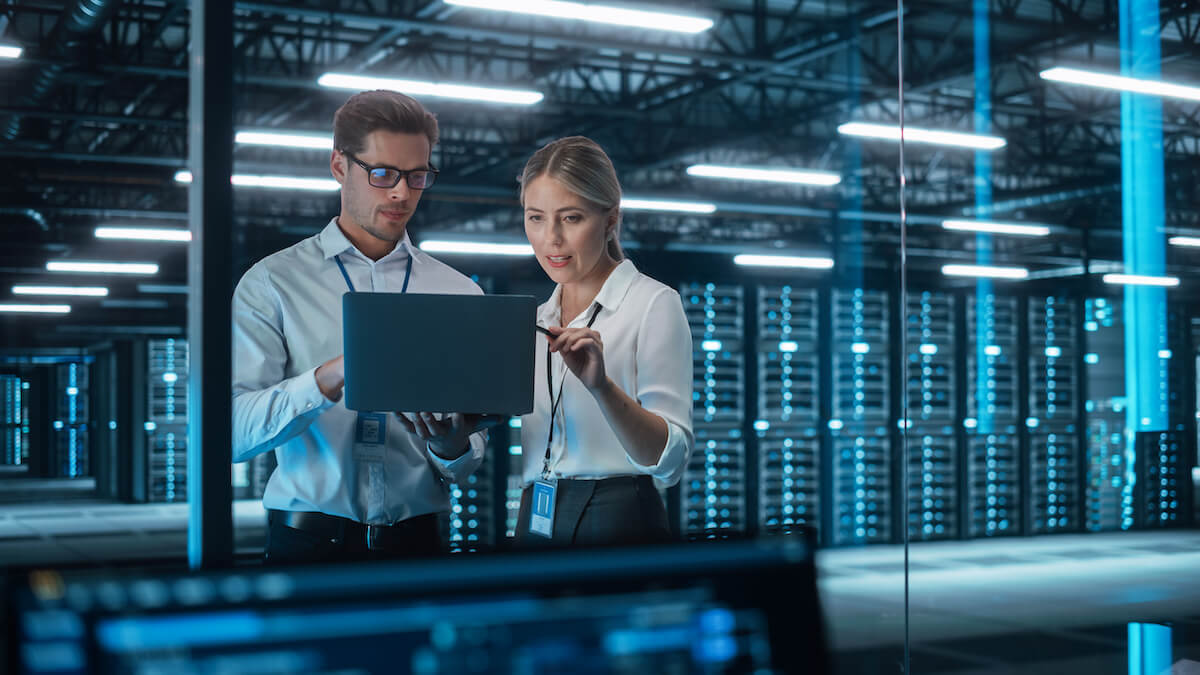
If your business relies more and more on outsourced service providers, it's crucial to take a closer look at how effectively your suppliers are managing their own business risks.
Operational risks in your supply chain can have serious financial, reputational, and legal consequences. When vendors’ critical business processes are disrupted, that system failure can affect your business too.
For example, many organizations use third-party service providers for technology-related projects or services. But if something goes wrong with one of these outsourced providers, your organization could be left holding the bag for your customers' financial losses.
These losses could range from the cost of repairing or replacing faulty equipment to the cost of compensating customers in the event of a data leak.
A bad outsourcing experience doesn’t just affect your bottom line — it can drag you into the court of public opinion too.
Examples of Vendor Operational Risks
We can’t say it enough: Your vendors’ risks can become threats to your own company.
Let’s say your outsourced IT system provider from our earlier example has weak cybersecurity practices. This can leave your company vulnerable to a breach in your own IT infrastructure. If this happens, it’ll become harder to deliver services to your customers, costing you in terms of both reputational risk and financial risk.
Take a recent example: In 2020, vendor Capgemini made a security error that led to a significant customer data leak and operational losses of about $7 million for a Singaporean gaming firm.
On top of lost revenue and opportunities because of downtime, situations like these leave your business open to other legal and financial consequences such as regulatory fines, litigation costs, and loss of customer trust and loyalty.
Other operational risk examples include:
- Contract breaches: When vendors don't fulfill their contractual obligations on time or within budget, it can be harder for you to deliver products and services to your customers.
- Security breaches: If a vendor can’t maintain robust security practices to protect customer data and other sensitive information in their possession, this can put your customers at risk and create liabilities for your organization.
- Service disruptions: Your business is at risk of financial loss when a vendor experiences a service disruption because of risk events including natural disasters, cybercrime attacks, human error, and more.
- Supplier bankruptcies or insolvency: A key vendor may go bankrupt for several reasons, including poor business decisions or unexpected changes in economic conditions. If this happens, your organization might not be able to deliver on your promises to your customers.
- Market risk: When markets change because of unforeseen economic circumstances or other external factors beyond your control, it can lead to volatility in the supply of raw materials and/or products from your vendors.
- Regulatory changes: Changes in regulatory requirements can negatively affect an unprepared supply chain, particularly if these changes lead to increased monitoring by your regulators. This can increase your administrative burden and lead to additional expenses as you implement the right controls and procedures.
What Causes Operational Risk in Supply Chains?
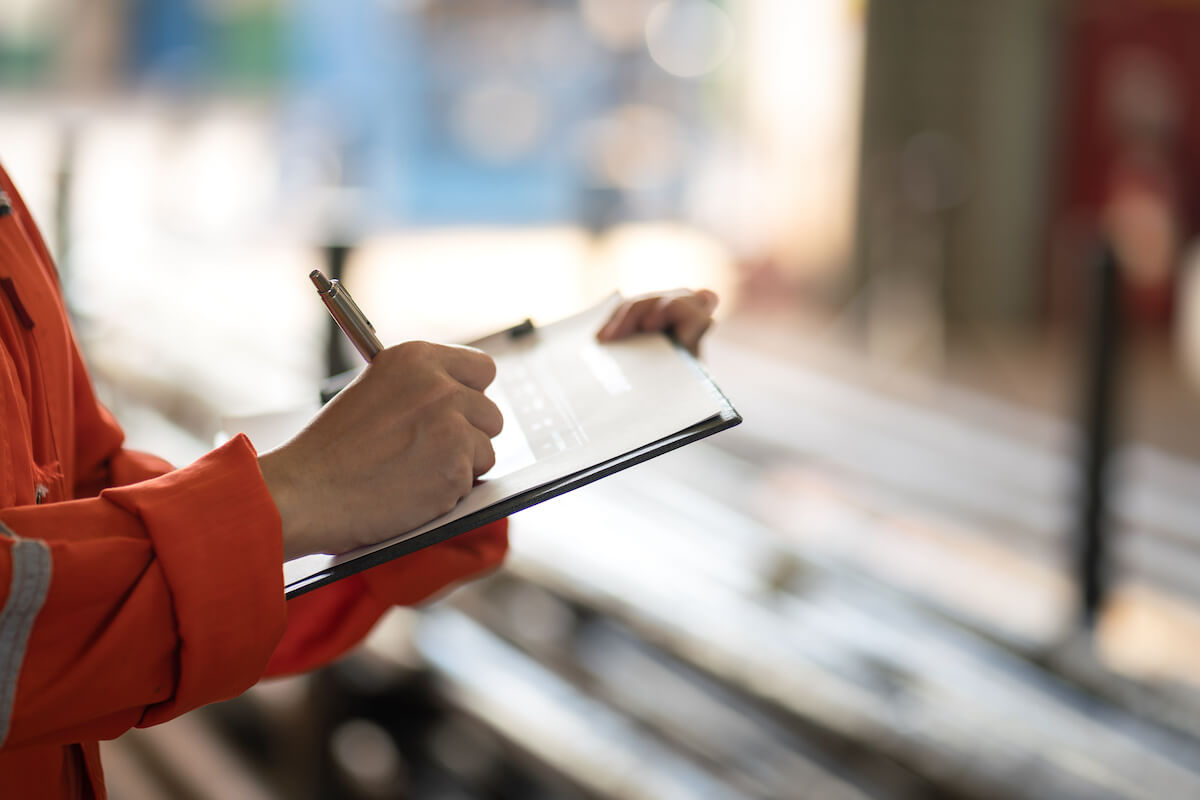
There are several factors that can influence an organization's ability to prevent and control losses due to operational risk factors, including:
- Lack of visibility: A lack of visibility over your third-party network makes it difficult to identify and manage specific risks. This is especially true if your company uses many service providers that aren't fully integrated into your vendor ecosystem.
- Improper or insufficient personnel training: A team's inability to accurately assess its vendors’ risk profiles can lead to procurement mistakes and a negative impact on vendor quality. Without the right supervisory input, the lack of qualified personnel to oversee your vendor management can also cause unsatisfactory relationships with vendors.
- Human error: If your organization isn't prepared to manage its third-party relationships effectively, it's easy for human error to creep in. Of course, careless mistakes can sink your vendor relationships as well.
- Weak risk management processes and controls: Poor risk management processes and a lack of internal controls can leave your business wide open to potential financial losses and other negative outcomes like internal fraud, theft, errors, and breach of contract.
- Reduced focus on compliance: If your senior management team has kept compliance on the back burner for your third-party management program, your firm may be subject to significant fines and other penalties.
- External risk events: Natural disasters, pandemics, acts of war or terrorism, external fraud, and climate risk can all contribute to your operational risk.
How to Reduce Your Organization's Operational Risk Exposure
Poorly assessed and managed risks are a drain on your business. But strong operational risk management processes will help to protect your business and allow you to better fulfill your commitments to customers and other stakeholders.
An effective operational risk management system should help to create a culture of risk awareness for decision-making within your organization. Once your team’s leveled up in terms of risk awareness, you’ll have more risk control in all areas of your business practices — and know how to meet regulatory and international standards.
While it's impossible to get rid of all risky business completely, here are some ways to identify and mitigate potential operational risks in your supply chain:
- Work with key stakeholders to develop your operational risk management framework: Building an operational risk management program starts with understanding your organization’s risk appetite and risk tolerance. Once you know the greatest areas of concern you need to address, you can decide on the right mitigation strategies to use in different business units.
- Use key risk indicators (KRIs): KRIs give your team quantifiable metrics for risk measurement. You can track these over time to understand when your risk might be increasing. For example, increased worker strikes could affect the production output of a manufacturing vendor or the ability to deliver goods on time for a logistics vendor. Both scenarios can wreak havoc on your profitability.
- Conduct regular vendor risk assessments: Regular vendor risk assessments help you see changing risk levels in your supply chain. The assessment process highlights high-risk vendors and areas for improvement so you can take steps to protect your business.
- Practice scenario analysis: Develop different loss event scenarios that could affect your business activities and prepare responses accordingly so that your team can respond quickly and effectively in real-time.
- Develop and implement a robust business continuity plan: Maintaining a strong business continuity plan helps you maintain control over critical business processes during difficult situations, helping to minimize any disruption to operations.
- Strengthen communication lines with your suppliers: Building strong relationships with your key suppliers will help your business to better manage its exposure to various risk factors. It’ll also help you see more potential risks across your supply chain, so both parties can better prepare for unexpected events.
- Keep evaluating your operational risk management program over time: Maintain your operational risk management programs with frequent self-assessment and reviews to ensure your risk management methodologies work just as you wanted them to.
Use automated vendor management platforms to reduce human error and increase risk visibility. Thoughtless mistakes can happen more and more as you place greater demands on your team. Those errors have huge repercussions and can cost an organization in compliance fines, reputation, and ultimately lost business. With automation and 24/7 monitoring, a central vendor management platform helps protect your organization by reducing human errors and offering greater visibility into your risk areas
Boost Your Vendor Operational Risk Management Processes With Certa
To minimize your vendor operational risk, it's vital to have a comprehensive understanding of your firm's unique operational risk environment. But assessing your business risk doesn't have to be a challenge.
Certa's third-party lifecycle management software is key for any organization looking to effectively manage their strategic risk program. Our fully customizable platform helps you automate and track the performance of your third-party vendors from supplier onboarding to ongoing task management.
With full spectrum risk coverage across all areas of your business, the platform will also empower your team to identify potential issues early and address them before they become a problem.
To streamline your vendor operational risk management, talk to our team today.