6 Steps To Mitigate Supply Chain Risks
As the cogs of the global economy turn with increasing speed and complexity, so too do the supply chains that keep businesses afloat. Their complexity and interconnectedness have grown exponentially, reflecting our increasingly globalized and digital world. Therefore, supply chain risk management has become an essential practice for every business. As a result, businesses must navigate various challenges and disruptions to maintain their operations smoothly.
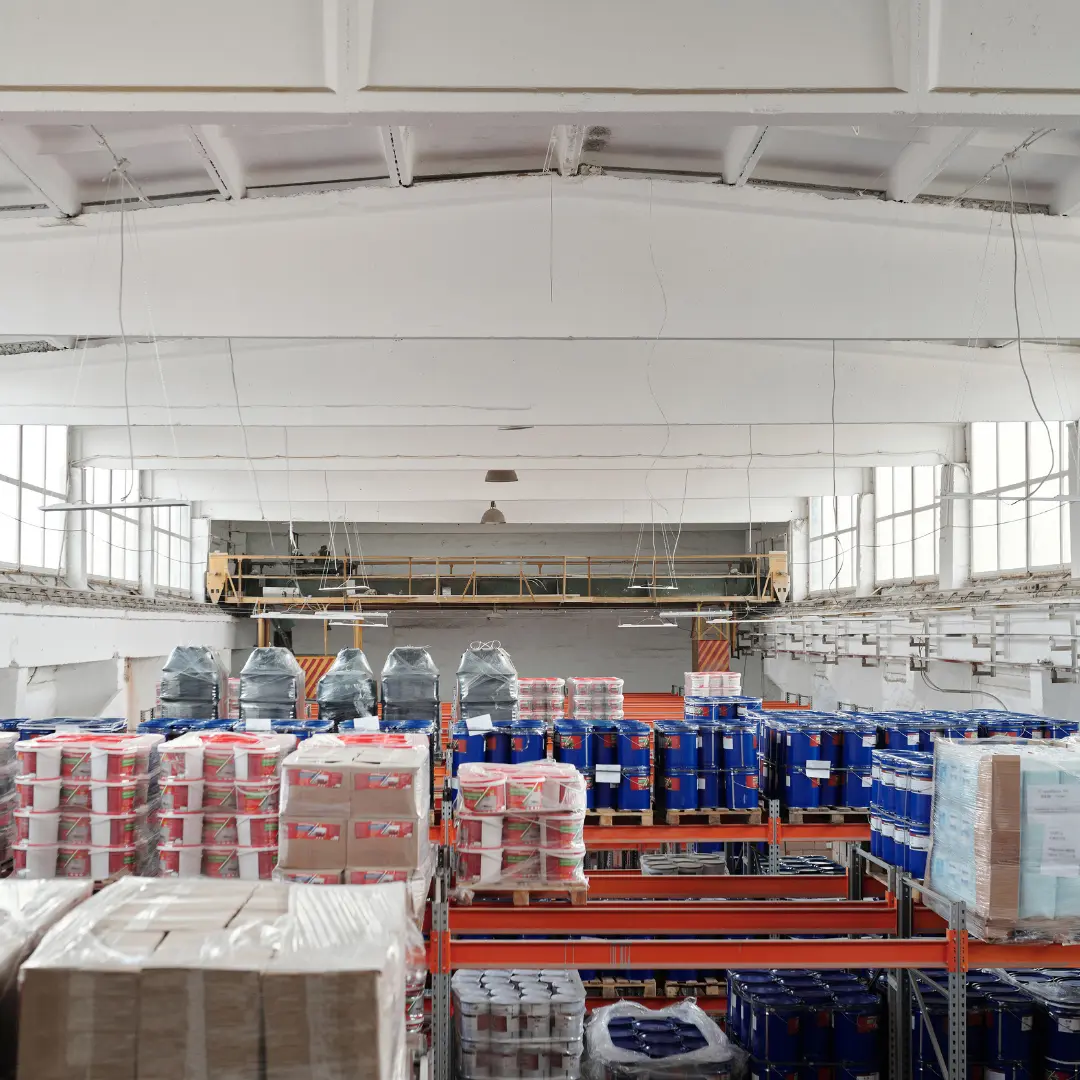
Understanding Supply Chain Risks
Primary Sources of Supply Chain Risks
The sources of supply chain risk are as diverse as the chains themselves. Geopolitical events, like trade disputes or political unrest, can abruptly sever a critical link in a supply chain. Natural disasters, too, can wreak havoc, paralyzing logistics and disrupting production. Logistical errors, such as flawed planning or human errors, may also introduce substantial risks. Lastly, the increased reliance on technology poses its own set of risks, including cyber threats and system failures.
Impact of Supply Chain Disruptions
Understanding the potential impacts of these risks is crucial for devising a comprehensive supply chain risk management plan. These disruptions can have far-reaching consequences, affecting everything from production timelines to financial stability. Evaluating these impacts helps organizations prepare and mitigate risks more effectively. Here’s a look at the primary impacts:
- Ripple Effects That Interrupt Production: Supply chain disruptions can cause immediate halts in production, which is just the tip of the iceberg. For example, a delay in receiving essential components like microchips can stall entire assembly lines, resulting in unmet production goals and workers being left idle. This disruption does not stop at a single point; it cascades throughout the supply chain, affecting downstream processes reliant on the initial outputs. Over time, these interruptions compound, leading to substantial reductions in operational efficiency and total production capacity. Companies may find themselves scrambling to find alternative suppliers or paying premium prices for rush orders, incurring higher costs and operational chaos.
- Increased Operational Costs: When there is a kink in the supply chain, operational costs invariably spike. Firms often have to find alternative sources for materials, generally at higher prices, or pay for expedited shipping to meet looming deadlines. Furthermore, storage costs may balloon if inventory must be held longer due to supply-demand mismatches. There are also increased labor costs involved with managing the disruptions. Workers may need to put in extra hours, or additional staff may need to be hired to ensure quality control and manage logistics under less-than-ideal production circumstances. These elevated costs can severely erode profit margins, putting significant financial pressure on businesses, especially smaller firms with less capital flexibility.
- Significant Delays in Delivery: Supply chain disruptions typically lead to significant delivery delays. For retailers, this means that products do not reach the shelves on time, leading to lost sales and customer dissatisfaction. Manufacturers face setbacks as delays in receiving raw materials push production schedules back, impacting their ability to meet order commitments. These delays can harm business relationships, particularly with partners who depend on timely deliveries for their operations. Over time, repeated delays can damage a company's reputation for reliability, making it harder to maintain or establish new business relationships.
- Financial Losses Impacting Profitability: The financial repercussions of supply chain disruptions extend beyond immediate increased costs. Firms can face lost sales due to stock shortages, incur penalties for not fulfilling contracts, or need to offer discounts on late products to move them quickly once they arrive. Moreover, the relational cost of such disruptions is high; companies often have to invest in improving services or compensating partners and customers for the inconveniences caused. Rebuilding trust and ensuring reliability to prevent future financial losses often requires substantial investments and strategic changes in operations.
Companies must assess these potential risks and develop strategies that enhance resilience and responsiveness in their operations. By understanding these critical areas of vulnerability, organizations can better shield themselves from severe financial harm and maintain operational continuity in the face of supply chain challenges.
Key Steps to Mitigate Supply Chain Risks
Now that we've explored the sources and impacts of supply chain disruptions, it's time to delve into the key steps of supply chain risk mitigation.
Risk Identification
Risk identification serves as the foundational step in any supply chain risk management framework. It involves a thorough analysis and understanding of every component within the supply chain, from the smallest supplier to the largest distribution hub. This process requires a deep dive into the complexities and dependencies that characterize the supply chain. By mapping out these relationships and flows, businesses can pinpoint areas of vulnerability that could potentially disrupt their operations. Key activities in this phase include gathering data from various sources, engaging with suppliers to understand their operational and financial stability, and assessing external factors such as geopolitical or environmental risks that could impact the supply chain. This comprehensive approach ensures that organizations are well-prepared to recognize and react to potential risks before they escalate into more significant issues.
Risk Assessment
After identifying potential risks within the supply chain, the next step involves a detailed risk assessment. This stage is crucial as it evaluates the potential impact and likelihood of each identified risk, enabling organizations to prioritize their response strategies based on the severity and probability of occurrences. Effective risk assessment involves quantitative and qualitative analyses to measure how different scenarios could affect the supply chain’s efficiency and security.
By understanding which risks could have the most substantial impact, companies can allocate resources more effectively and focus on mitigating significant threats. This prioritization helps in building resilience and ensuring sustainability in the face of uncertainties, thus safeguarding the supply chain against a wide array of potential disruptions.
Supplier Relationship Management
In supply chain risk management, maintaining strong and transparent relationships with suppliers is essential. This management facet focuses on developing trust, ensuring transparency, and fostering mutual benefits in supplier interactions. By implementing robust supplier relationship management strategies, including regular communication and collaborative problem-solving, companies can enhance their responsiveness to supply chain issues. Diversification of suppliers is another critical strategy that reduces dependence on a single source, thereby minimizing the risk of major disruptions. Such relationships are crucial for achieving a resilient supply chain, as they help in understanding the suppliers’ capabilities and limitations, allowing for quicker adaptations in response to changing conditions.
.webp)
Risk Mitigation Planning
Creating an effective risk mitigation plan is crucial for the resilience and longevity of supply chains. As businesses face an increasingly volatile global market, understanding and preparing for potential risks is vital. The following steps outline a comprehensive approach to developing a risk mitigation plan, ensuring each measure is specifically tailored to address the identified vulnerabilities effectively:
- Identifying Potential Risks: As discussed previously, a crucial first step in risk mitigation is to thoroughly assess and identify potential risks within the supply chain. Once identified, these risks are categorized based on their likelihood and potential impact, which helps prioritize mitigation efforts.
- Designing Flexible Strategies: Strategies might include diversifying suppliers to avoid reliance on a single source, investing in technology for better data visibility across the supply chain, or developing contingency plans for critical operations. The flexibility of these strategies is key; they must be capable of evolving as new information emerges and as the business and its environment change. This adaptive approach ensures that the supply chain remains robust against both foreseeable and unforeseeable challenges.
- Incorporating Resilience Tactics: Building resilience into the supply chain involves incorporating specific tactics designed to reduce vulnerability and enhance the ability to respond to disruptions. This can include establishing alternative supply routes to circumvent potential blockages, increasing inventory buffers to protect against supply delays, and forging new supplier agreements to secure additional resources. Additionally, resilience can be bolstered by improving communication and collaboration across the supply chain, ensuring all stakeholders are aligned and can act quickly when issues arise. These tactics make the supply chain more flexible and responsive, thereby improving overall stability and performance.
- Utilizing Scenario Planning: Scenario planning plays a critical role in testing the effectiveness of the strategies and tactics outlined in the risk mitigation plan. This process involves simulating different risk scenarios to observe how the supply chain would respond under various conditions. The insights gained from these simulations help identify gaps in the strategies and provide opportunities for refinement. Scenario planning also helps in training personnel to react to disruptions and in refining communication protocols, ensuring that when real disruptions occur, the response is swift and effective.
- Implementing Proactive Measures: The final step in the risk mitigation plan is the implementation of proactive measures that equip businesses to manage and navigate uncertainties effectively. This includes the adoption of advanced analytics for real-time decision-making, regular reviews and updates of the risk mitigation plan, and ongoing staff training. By proactively addressing potential issues before they arise, businesses can maintain operational integrity and ensure the continuity of supply chain operations under various scenarios.
A well-structured risk mitigation plan is a strategic asset for any business that relies on complex supply chains. By following these detailed steps, organizations can enhance their ability to withstand disruptions, maintain continuous operations, and secure a competitive advantage in the face of uncertainties. This proactive approach not only safeguards the supply chain but also supports the overall strategic objectives of the organization.
Use of Technology in Risk Mitigation
The integration of advanced technologies such as artificial intelligence (AI) and blockchain is transforming supply chain risk analysis management. AI applications can predict potential disruptions by analyzing vast amounts of data on supply chain activities and external market conditions. This predictive capability allows companies to react swiftly to upcoming challenges. Meanwhile, blockchain technology enhances transparency and traceability within the supply chain, providing stakeholders with real-time data on the movement and status of goods. This increased visibility helps in monitoring compliance, reducing fraud, and improving the overall reliability of the supply chain. Together, these technologies empower businesses to better manage risks and adapt to new developments efficiently.
Regular Audits and Monitoring
Regular audits and continuous monitoring are critical in the ongoing management of supply chain risks. These activities involve systematic reviews and assessments of the supply chain processes to ensure compliance with established standards and to identify any new or evolving risks. Frequent monitoring allows companies to keep a pulse on the operational health of their supply chains and react quickly to any signs of disruption. This proactive approach helps in maintaining the effectiveness of the risk management strategies in place. Regular audits also foster a culture of continuous improvement, as insights gained can lead to enhancements in risk management practices, ensuring that the supply chain remains robust and responsive to changing market dynamics and operational challenges.
Supply Chain Risk Mitigation
Overcoming Geopolitical Disruptions
A notable example of enhancing supply chain resiliency is when a company successfully navigates significant geopolitical risks. Through diligent efforts in supply chain risk assessment and management planning, the company diversified its supplier base, reducing dependence on suppliers from politically unstable regions. This strategic decision proved crucial in mitigating potential disruptions and ensuring the continuity of their supply chain operations.
Triumph Over Natural Disasters
In the face of a natural disaster, another company demonstrated its resiliency by effectively utilizing supply chain risk management software. With this technology in place, the company swiftly rerouted shipments to alternative routes and locations, effectively mitigating disruptions caused by the natural disaster. The company's preparedness and ability to swiftly adapt underscored the value of proactive risk mitigation planning and the importance of having robust contingency plans in place.
.webp)
In today's interconnected and fast-paced global economy, the importance of understanding and mitigating supply chain risks cannot be overstated. Effective supply chain risk management is no longer optional but has become essential for businesses to thrive. It requires constant vigilance to identify and assess potential risks, thorough planning to develop robust contingency measures, and the ability to swiftly adapt to changing circumstances. By embracing the right strategies and utilizing appropriate tools and technologies, businesses can build resilient supply chains capable of withstanding even the most significant disruptions. This proactive approach to supply chain risk management not only safeguards operations but also enhances customer satisfaction, protects brand reputation, and ensures long-term success in an increasingly volatile and uncertain business landscape.
The challenges of managing supply chains in a complex, interconnected world may seem daunting. However, by understanding the risks, devising comprehensive risk mitigation strategies, and harnessing modern technology, businesses can build resilient supply chains. We urge you to examine your supply chains for potential risks and consider implementing the strategies discussed here. By doing so, you too can contribute to a more resilient global economy.